Thermal Processing Handbook
Drying Technologies for Material Processing
Thermal Processing Overview
Thermal processing equipment is vital technology in the manufacturing process of foods, pharmaceuticals, chemicals and numerous other types of applications. Thermal processing refers to changing the temperature of a material with the intention of changing its state in some way. This handbook focuses on various examples of direct and indirect thermal processing techniques. Direct methods are based on generating heat/energy within the material itself, where indirect methods rely on transfer heat generated from another source and applied to the material either through conduction or convection.
Different approaches for temperature modifications are appropriate depending on the application. Materials are thermally processed during production for a variety of reasons including, but not limited to:
- Activating chemical processes for mixes and combinations of materials
- Drying of materials
- Cooking or other types of alterations available through thermal reactions
- Sterilization or removal of microbes or other bacteria
- Crystallization and degassing
In many types of applications, thermal processing must be extremely precise, and the energy applied should be uniform. Inconsistent temperatures can cause poor material results including overheating, burning, sticking, case hardening and other quality problems within the final products.
Indirect heating is a traditional form of thermal processing. By utilizing steam or hot air, these methods heat material from the outside or indirectly. Indirect heating can be particularly effective in ovens, conveyer belts, jacketed cookers or thermal screws. These types of technologies are utilized in continuous applications where the materials are exposed to the heating element for a fixed amount of time while they are in motion through their processing. In batch applications, materials can be placed in ovens or industrial heating drums, mixers and kettles, which also agitate the materials. Batch processing allows for varying heating times, measurement of the material during heating and mixing for a more uniform material temperature.
Direct heating technology refers to methods like industrial microwave. Microwaves generate heat directly at the molecular level, thereby heating the entire material, rather than traditional methods that work from the outside in. Similar to indirect heating, microwaves can be applied in continuous or batch processes, but a key point of differentiation is microwave’s ability to immediately provide precise temperature control.
APPLICATIONS
Every day, thousands of industrial applications require thermal processing of some sort. This handbook will focus on drying, as it represents a large segment of thermal processing common to food, chemical, pharmaceutical/nutraceutical and biomass.
Many of today’s powdered products, highly nutritional processed foods, pharmaceutical and some organic products would not be possible without advances in thermal processing precision. As the quality of drying and processing advances, flavor, quality, density and form of these products can all be improved.
Sample applications include:
- Cannabis
- Carbon products
- Consumables that require elimination of bacteria
- Crystalized materials
- Dried fruits, meats and other types of dried foods
- Drying of moist products with low thermal conductivity
- High-precision/specialty chemicals
- Nanocrystal and nanomaterials
- Organic solvents
- Pasteurization
- Pharmaceutical APIs: Active Pharmaceutical Ingredients
- Powders for pharmaceutical and food products
- Roasting
- Stationary drying of thick layers
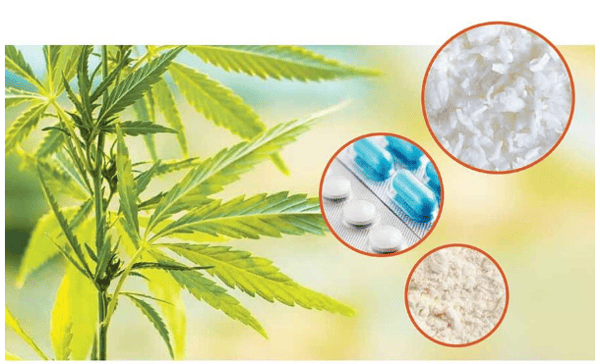
THERMAL PROCESSING OPTIONS
Drying technologies fall into the following categories:
- Fluid Bed
- Rotary
- Spray
- Tunnel
- Freeze
- Flash
- Microwave
Each of these options has advantages and disadvantages, outlined below.
Fluid Bed
Fluid bed dryers work by allowing heated, high-pressure air or process gas to flow through a bed of material in an upward direction at a velocity greater than the settling rate of the particles. At this state, the bed is fluidized and the particles begin to dry. While fluid bed processing is an indirect heating method, it is effective for drying granular solids because each particle is completely surrounded by the drying gas, giving a consistent result. However, the volume of air in the fluidizer must be kept constant, so it may be inefficient for smaller batches. Vibration may be added to assist with the fluidization of more difficult materials. To improve energy efficiency in fluid bed dryers, exit air is sometimes recycled and reused for heating.
Advantages of Fluid Bed Dryers:
- Shorter drying times than static bed convection
- Reduced contact time for drying
- High rates of moisture removal due to excellent gas-particle constants, resulting in high heat and mass transfer rates
- Ability to control the exposure time of the materials to heat
- Ease of control
- Lower capital and maintenance cost
- For light materials, the air flow may raise them above the bed for even heating
- Continuous and batch models are available for different applications
Disadvantages of Fluid Bed Dryers:
- The air temperature range is limited for drying
- Significant effort and expense involved in commissioning and parameter optimization
- High energy consumption
- Potential for product attrition and agglomeration
- Not appropriate for materials that are liquid, too wet, sticky or adhesive
- Many models cannot dry fine powders
- Many models are difficult to clean
- Unsafe for flammable or toxic materials
- Not always effective for removing organic solvents
- The vigorous movement of the particles in the hot drying air may lead to the generation of electrostatic charge
Rotary/Drum Dryers
Rotary drum dryers use rotational cylinders that allow materials to cascade inside the drum while heat is applied in order to extract moisture resulting in a dry product. Drums can produce sheets, powders and flakes from the materials being handled.
Drum dryers are differentiated from rotary kilns by the temperatures at which they heat materials. Generally, drum dryers operate at temperatures of 600°–1400°F where rotary kilns are typically refractory lined with a brick or other lining and operate from 1000°–3000°F in order to create a chemical reaction.
Advantages of Drum Dryers:
- Low maintenance costs
- Simple installation and fast commissioning
- Low wear and low replacement part requirements
- Minimal cost and effort for the supplied air equipment with direct installation of the burner at the dryer casing
- Low specific electrical energy requirement
- Ability to compress product for sheet applications
- Appropriate for drying liquids without loss of materials
- Ability to handle viscous materials
- Insensitive to changes in the particle size
- Convenient powder and flake sizes
- Ability to handle variations in the moisture content and throughput
- Easy to operate
- Single dryer can be used for different mixes
Disadvantages of Drum Dryers:
- Long heating times
- Safety distance required for high-temperature equipment
- Large physical footprint
- Low thermal efficiency resulting in high heat loss
- Potential for material attrition
- Unable to process salty or corrosive materials
- Counter-flow applications are limited to coarse-grained materials
- Some products are difficult to scrape from the drum (high sugar content)
- Solid materials are only partially de-dusted in drum dryer
- Significant cool-down period required in order to clean or maintenance